Improving protection and agricultural productivity
thanks to plastic films with graphene oxide
The applications of plastic materials are very diverse, for use in agriculture, the formulation and development of plastic films for greenhouse covers, macrotunnels and microtunnels and for soil padding stands out. Among the most used plastic materials are Linear High Density Polyethylene (HDPE), Ethylvinylacetate (EVA), in the case of covers for structures, and Linear Low Density Polyethylene (LLDPE) as the main polymer for the manufacture of films for floor mulch.
Plastic films with the capacity to convert and transmit solar energy are materials of great interest for photothermal applications in agriculture. In this sense, the development of mulch films with good mechanical properties and photothermal conversion properties suitable for the agricultural field is still an urgent demand.
In recent years, graphene has attracted considerable attention due to its unique sheet structure, its extraordinary photothermal properties, and its mechanical properties.
To improve the solar conversion efficiency of plastic films, carbon-based nanomaterials such as: graphene (GnP), graphene oxide (GO) and reduced graphene oxide (RGO) can be incorporated, because they have excellent light absorption capacity with a wide spectral range (from ultraviolet to near infrared), and can convert light energy into heat energy (photothermal property).
Recent developments in the formulation of films, look for the blocking of UV radiation, the fluorescence effect, ultra-thermal films and more impermeable films. Other key properties desired in plastic films are mechanical resistance (greater durability), optical properties and anti-drip effect.
Recent studies have reported the values of water vapor permeability (WVP) in plastic films composed of graphene at different concentrations (0, 2, 4, 6 and 8% by weight). Where it was found that the water vapor permeability in the films continuously decreases (improves the barrier property) as the concentration of graphene in the films increases. This evaluation was carried out at different relative humidity (RH) percentages, where good performance in the barrier property could be observed at different humidity percentages (32%, 55% and 76%), see Fig. 1. When the graphene content increases up to 8% by weight, the WVP of the composite films decreases from 3.9 x10-10, 5.5 x10-10, and 7.6 x10-10g/m h Pa to 0.6 x10-10, 0.8 x10- 10, and 1.2 x10-10g/m·h·Pa at 32%, 55% and 76% relative humidity, respectively. This decrease in permeability is associated with the fact that graphene forms barriers at the molecular level in plastic films, giving rise to more tortuous paths for the diffusion of water vapor molecules or oxygen molecules, limiting their transportation through the plastic film. This reduction can also largely prevent evaporation and loss of water, a very valuable resource in these times of scarcity.

In Fig. 2, the stress curves of the graphene composite films are shown. It was found that the tensile strength of the films with graphene (2-8% by weight) increased up to 22.6 MPa compared to the virgin or control film (18.3 MPa). While the Young’s Modulus continuously increased from 95.7 to 171.2 MPa with the graphene content from 0 to 8% by weight, these results show an improvement in mechanical strength.
From the point of view of the horticulturist, the most relevant mechanical properties are: resistance to traction, tearing and impact. Tensile strength assesses the film’s ability to withstand tensile stresses and is very important when mounting the film to the padding.
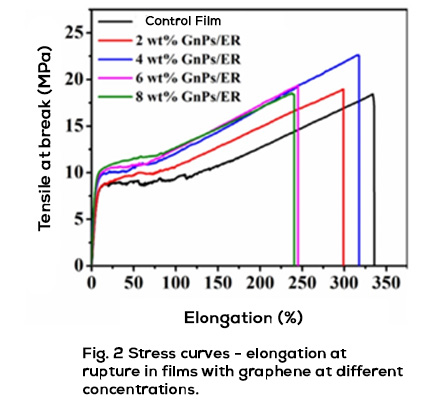
Regarding advances in polymeric compounds with graphene and derivatives in solar energy conversion applications. Fig. 3 illustrates the photothermal conversion efficiency of the films on the soil surface. The photothermal conversion efficiency of graphene composite films was observed to gradually increase with graphene content.
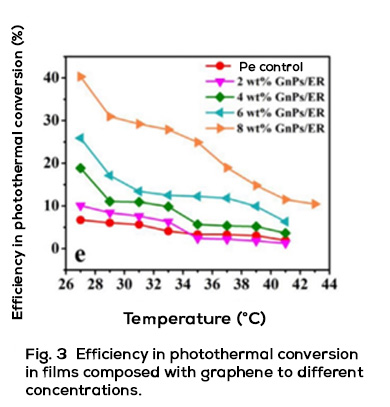
The films composed at concentrations of 2,4,6 and 8% by weight of graphene, showed a higher photothermal conversion efficiency (10.1, 19, 26 and 40.3%) than the control film (6.7%) for a temperature of 27° C, indicating that graphene composite films can effectively adsorb light and can convert light energy into heat input that can rapidly increase soil temperature.
Interestingly, all graphene composite films showed better photothermal conversion performance to increase soil temperature compared to the control group. These results indicate that the composite films have good mechanical properties and adequate photothermal conversion properties that can potentially be used in mulch films to improve soil temperature and maintain soil moisture, which is beneficial for plant growth and production. agricultural crops.
Currently Energeia – Graphenemex®, a leading Mexican company in Latin America in research and production of graphene materials for the development of applications at an industrial level, through its Graphenergy Masterbatch line, has developed and sells a wide range of masterbatches with graphene (graphene concentrate), with polymers widely used in agriculture and/or horticulture, such as LLDPE, LDPE, and HDPE. Our Masterbatches are granulated materials that act as multifunctional reinforcements for the production of more resistant plastic films with lower permeability and with a high degree of photothermal conversion.
References
- Melt processing and properties of linear low density polyethylene-graphene nanoplatelet composites. P. Khanam, M.A. AlMaadeed, M. Ouederni, E. HarkinJones, B. Mayoral, A. Hamilton, D. Sun. 2016, Vacuum , Vol. 130, págs. 63-71.
- Sun, Q., Geng, Z., Dong, J., Peng, P., Zhang, Q., Xiao, Y., & She, D. (2020). Graphene nanoplatelets/Eucommia rubber composite film with high photothermal conversion performance for soil mulching. Journal of the Taiwan Institute of Chemical Engineers.
- Effect of functionalized graphene on the physical properties of linear low density polyethylene nanocomposites. T. Kuila, S. Bose, A. K. Mishra, P. Khanra, N. H. Kim, J. H. Lee. 2012, Polymer Testing, Vol. 31, págs. 31-38.