Innovation in corrosion protection:
graphene oxide technology
Corrosion is the greatest challenge that many industries in the world must face. Currently, there is a wide variety of coatings on the market for protection against corrosion. However, most of these coatings do not have the physicochemical characteristics necessary for good performance. These coatings does not have perfect barriers and eventually fail, their chemical resistance depends on their impermeability to chemical substances, and with it their resistance to abrasion and their adhesion capacity.
Currently Energeia – Graphenemex®, a leading Mexican company in Latin America in the research and production of graphene materials for the development of industrial applications, has a wide range of coatings through its Graphenergy line.
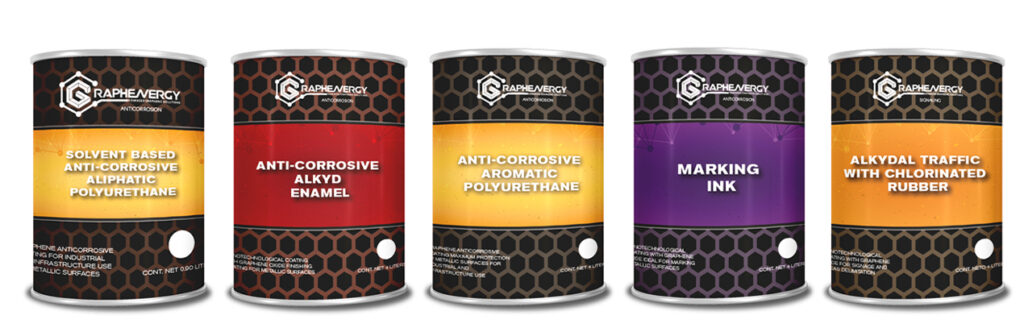
Graphenergy is the line of nanotechnological coatings with graphene oxide, which has a complete portfolio of high-performance anticorrosive coatings for Industrial and Infrastructure maintenance.
Taking into account that the infrastructure or industrial equipment may be exposed to environments with different degrees of corrosion (intermediate or extreme), the use of Coating Systems for corrosion protection is recommended, Graphenergy offers the following alternatives:
1. ALKYD SYSTEM
Recommended for intermediate or mild corrosion environments (intermediate corrosive or aggressive conditions). This system is weather resistant and provides anticorrosive protection.
This system is made up of a primer and alkyd-type enamel, ideal for the protection of metal surfaces and industrial infrastructure, both for interiors and exteriors. Provides high anticorrosive protection, resistance to UV rays and provides extraordinary adherence to the substrate. It is recommended for non-coastal areas or where humidity conditions are not high.
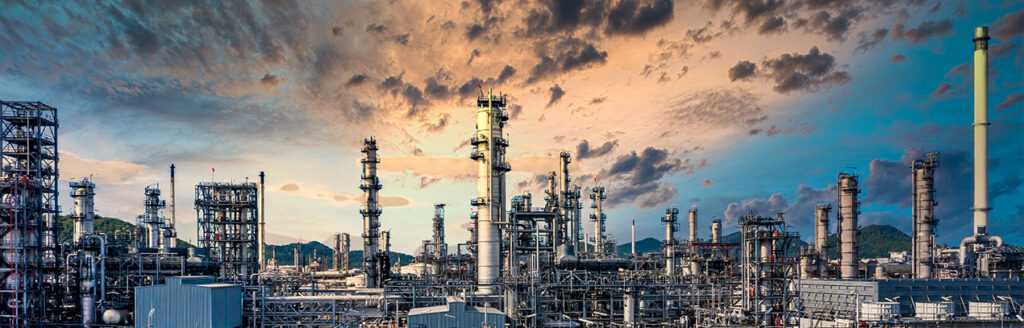
2. EPOXY-POLYURETHANE SYSTEM
Designed for severe or critical environments, in which the infrastructure or equipment and/or some other protected element is exposed to UV rays and an industrial atmosphere with high contamination (highly corrosive vapors).
This system is made up of an epoxy primer and Polyurethane (finish). Coatings designed for the protection of metal surfaces exposed to highly corrosive and chemical environments. Both coatings offer high adhesion, extraordinary chemical resistance, high abrasion resistance, resistance to UV rays, and impermeability, to improve the life of any metal surface or installation and reduce maintenance costs.
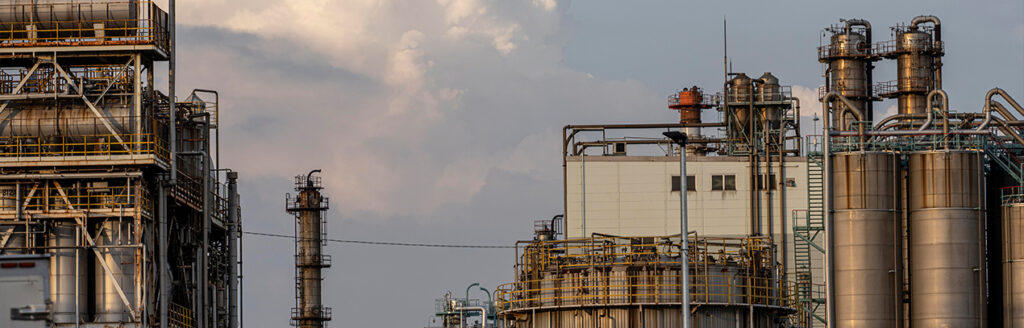
Graphenergy anticorrosive coating systems have many benefits, which include:
- Higher performance than existing coating technologies on the market today.
- Fewer applied coating layers are required and with higher anti-corrosion protection.
- Coatings with greater adherence to the substrate.
- Coatings with greater chemical resistance and high thermal resistance.
- Coatings with greater impermeability and non-stick effect.
When a coating system is selected, the influence of the environment to which it will be exposed and the final appearance that is sought and some other considerations that the system must perform, and its maintenance must be taken into account.
On the other hand, another decisive factor that determines the selection of the first anticorrosive to be used and consequently the coating system is the physical state of the metal surface to be coated and/or the surface treatment or preparation that can be given.
Referencias
- Fengjuan Xiao, Chen Qian, et al., et al., Progress in Organic Coatings, 125, 79-88 (2018); doi.org/10.1016/j.porgcoat.2018.08.027
- Karolina Ollik and Marek Lieder. Review of the application of graphene-based coatings as anticorrosion layers. Coatings 2020, 10(9), 883. 2020.
- Zhang J., Kong, G., Li S., Le Y., Che C., Zhang S., Lai D., Liao X. Graphene-reinforced epoxy powder coating to achieve high performance wear and corrosion resistance. 20:1448-4160, 2020.