Graphene, the material of the future
in coatings and paints industry
Graphene is currently the most revolutionary nanotechnological additive in the coatings and paints industry.
Coatings are regularly used for decorative purposes and for surface protection, especially for protection against corrosion, humidity, fouling, mechanical wear, among others. At a commercial level, there is a wide variety of coatings based on different types of resins and additives, their efficiency is generally associated with an increase in cost. However, the coatings still have low resistance to corrosion, abrasion and limited chemical and thermal resistance.
Therefore, the coatings industry, like many other industries, is constantly researching and developing new technologies for the formulation and application of new and better coatings.
Since 2004, when the graphene nanomaterial was first isolated, scientists in the coatings industry have been looking for ways to use graphene as an additive to improve the performance and technology of coatings in different application areas.
Graphene has unique properties, mainly attributed to its structure in the form of two-dimensional (2D) sheets, formed by carbon atoms linked in a hexagonal manner and a thickness of one carbon atom. This nanomaterial has extraordinary properties, which include high electrical and thermal conductivity, and high mechanical resistance. In addition, it possesses other distinctive properties, including gas impermeability, chemical resistance, antibacterial potential, and high surface area.
Graphene’s carbon-based composition and its compatibility make it a viable additive for organic polymeric coatings.
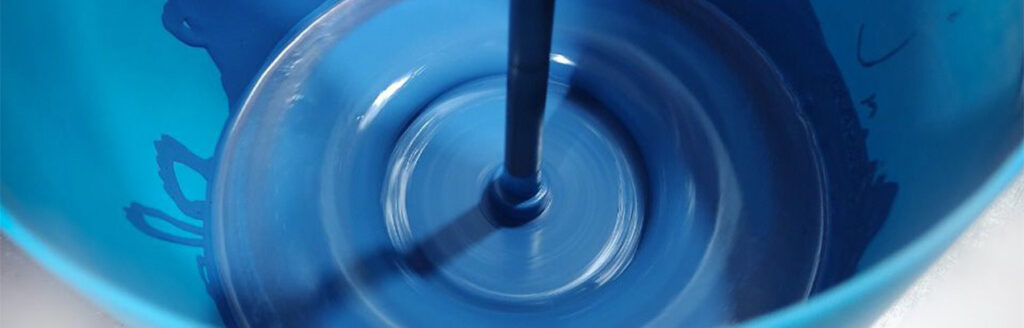
Among the advantages offered by the use of graphene is its ability to incorporate new or improved characteristics in the coatings. Different types of multifunctional coatings can be developed, such as:
- Anticorrosive coatings
One of the main uses of graphene coatings is protection against corrosion. Graphene creates pathways that are very tortuous, preventing water and oxygen molecules and/or chemical agents from diffusing to the surface of metal-based materials, resulting in metal protection against oxidation and corrosion. corrosion.
- Fire retardant coatings
Conventional additives based on halogens (bromine and chlorine), as well as phosphorous, melamine and inorganic compounds, are used to improve the fire resistance of coatings, however, these materials are toxic to humans and the environment. On the other hand, the high content of these flame retardants can cause the deterioration of other properties in the coatings.
Therefore, the application of graphene as a new additive in coatings can reduce or eliminate the use of conventional flame retardant additives, it can also provide the coating with better performance against extreme temperatures for a longer time and with better mechanical stability.
- Coatings resistant to wear or abrasión
Graphene has proven to be a potential candidate for wear, abrasion and scratch resistant coatings. Graphene is the lightest material and two hundred times more resistant than steel, in addition, graphene has a high capacity to withstand large pressure differences and high mechanical resistance.
- Antifouling coatings
Graphene is a good candidate for use as an anti-stick agent. Its application reduces the problem of fouling and the deposition of organic and inorganic materials in the hulls of ships, ships or marine vessels, oil platforms, among others. This type of application is mainly attributed to the hydrophobic (water repellent) and barrier properties of graphene.
- Antimicrobial coatings
The use of graphene or graphene oxide sheets as an antimicrobial agent is innovative, since there are studies that have shown a strong antimicrobial activity against a wide variety of microorganisms, including Gram +, Gram – bacteria and fungi.
Associated with the fact that graphene materials are capable of penetrating the cell membrane of microorganisms, producing oxidative stress and inhibiting their reproduction.
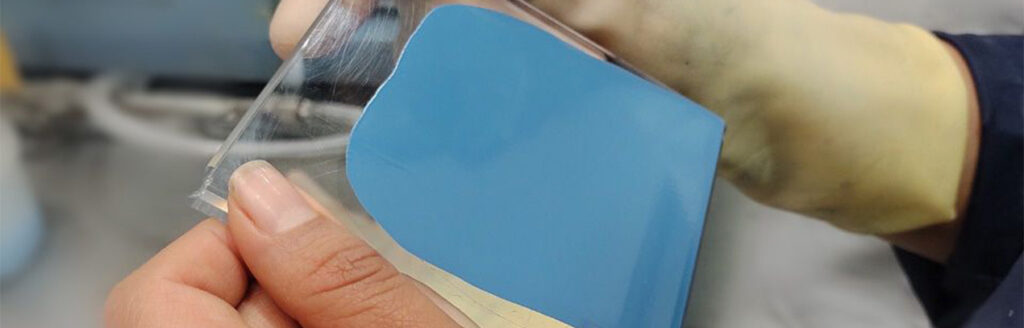
Globally, research and development of graphene-based coatings continues. Currently there are several companies and institutions that have made improved formulations with graphene for coatings, among which the following stand out:
- Applied Graphene Materials, based in the United Kingdom, in collaboration with the American company Sherwin-Williams, are developing graphene-based anticorrosive paints. Its objective is to incorporate graphene in different formulations, especially in maritime paint for use in ship hulls to protect them from corrosion.
- The Sixth Element Materials, a Chinese company that focuses on the research, development and sale of graphene materials, has launched a graphene-zinc-based anticorrosive primer for offshore wind power towers.
- Graphenstone, a Spanish company, has developed ecological paint that combines graphene and lime technology. Obtaining paints with greater resistance, flexibility, quality and a longer life span compared to conventional lime-based paints.
Energeia – Graphenemex®, a leading Mexican company in Latin America in the research and production of graphene materials for the development of industrial applications, through its Graphenergy line, has launched a wide range of nanotechnological coatings with graphene. These coatings offer high anticorrosive and antimicrobial protection. In addition, it provides high resistance to wear, resistance to UV rays, impermeability and extraordinary adherence, in order to improve the useful life of any surface or installation and reduce maintenance costs.
Graphene coatings, in addition to having anticorrosive protection, can provide greater chemical resistance, UV resistance, higher thermal performance in a wide range of temperatures, as well as more flexible and crack-resistant coatings.
References
- DuMée, L.F., et al., Carbon, 87, 395–408 (2015); doi:10.1016/j.carbon.2015.02.042.
- Wang, E.N., et al., Nano Lett., 15 (5), 2902–2909 (2015).
- J. Chen, H. Peng y X. Wang, Nanoscale, vol.6, pp. 1879-1889, 2014
- Md J. Nine, Martin A. Cole, Diana N.H. Tran, and Dusan Losic, J. Mat. Chem. A, 2015.
- Sachin Sharma Ashok Kumar, Shahid Bashir, K. Ramesh, S. Ramesh, Progress in Organic Coatings, 154, (2021)