Reinforced Concrete:
Why Choose Fibers with Graphene Oxide?
Fiber reinforced concrete is an improved version of conventional concrete characterized by better performance against cracking, deformation, fatigue and impact. It is widely used for the manufacture of industrial and commercial floors, tunnels, slopes, tanks, shotcrete, prefabricated and in some cases as a replacement for the electrowelded mesh of floors, but not as a substitute for the reinforcing steel of structural columns, load-bearing walls. or suspended beams. Unlike concrete reinforced with steel structures, fibers represent a discontinuous and homogeneous three-dimensional reinforcement within the concrete mixture that allows it to have the same characteristics at each point of the structure.
Of the extensive classification of fibers in terms of materials, lengths, thicknesses and geometries, the main competition is between steel fibers and polypropylene fibers, because both materials increase the toughness of concrete and allow it to continue absorbing loads before collapse. The difference is that steel fibers control cracking during the setting of the concrete and after hardening, they have great tensile strength and do not deform, but rather absorb energy and transform it into an internal stress; characteristics that make them very useful for use in concrete exposed to high loads. Polypropylene fibers contribute to the control of cracks due to plastic contraction, external loads, temperature, or drying contraction and, although its tensile strength is lower than steel, its deformation capacity allows it to absorb large loads without failing. They are less expensive, easier to handle and are generally indicated for lower load concretes.
Although the mechanical properties of steel fibers are superior to those of polypropylene and subject to the characteristics of the project and the applicable regulations, there are other technical differences that are worth considering when selecting:
Durability- The steel fibers within the concrete usually remain stable and isolated from the external environment, however, when this insulation is broken either by capillarity, microcracking or by a change in the pH of the concrete, the fibers become susceptible to corrosion, whose oxidation in the future will be responsible for the loss of adhesion with the concrete. The advantage of polypropylene fibers is that they are suitable for placement in humid and marine environments thanks to their chemical stability, resistance to corrosion and degradation.
Volumetric weight- The amount of polypropylene fibers per kilogram of weight is greater than those contained in one kilogram of steel fibers. This means that, to have a similar distribution, approximately between 5 and 8 kg of metallic fibers should be dosed for each kilogram of polypropylene fibers and, although the volumetric weight can be considered irrelevant for performance, the cost and handling of the product can be two interesting variables.
Adhesion – The adhesion or interfacial bond between the fiber and the concrete is essential for the long-term success of the structure and is quantified as the force necessary for the fiber to be torn from the concrete matrix or undergo rupture. In steel fibers, their adhesion depends mainly on their morphology and length; however, polypropylene fibers, in addition to facilitating the manufacture of different configurations, can also be chemically modified to improve their adhesion.
Distribution- Depending on the quantity dosed, steel fibers can form “hedgehogs” or leave spikes on surfaces, posing risks during handling and after placement. A disadvantage of polypropylene fibers is their hydrophobicity or incompatibility with water, this means that when the mechanical mixing of the fibers is carried out within the concrete composed of water, cement and aggregates, they can agglomerate and cause clumps, especially at dosages. elevated; Consequently, poor distribution, aggregation or formation of air spaces within the concrete will have a negative impact on its adhesion and, therefore, its performance.
Fire resistance – In the event of a fire, concrete can exhibit explosive detachment or “spalling” behavior, which consists of the violent expulsion of fragments due to the increase in pressure exerted by the release of water vapor until detachment occurs when the pressure exceeds the tensile strength of the concrete. Polypropylene microfibers melt at temperatures between 160 and 170° C, therefore creating interconnected channels that increase the permeability of the concrete and help release moisture and internal pressure.
The Mexican company Energeia-Graphenemex®, through its Graphenergy Construction division, takes advantage of the benefits of graphene nanotechnology to improve the characteristics of conventional polypropylene fibers; Its specialized formula allows obtaining individual filaments with greater mechanical and thermal resistance, better distribution and greater adhesion within the concrete compared to common fibers.
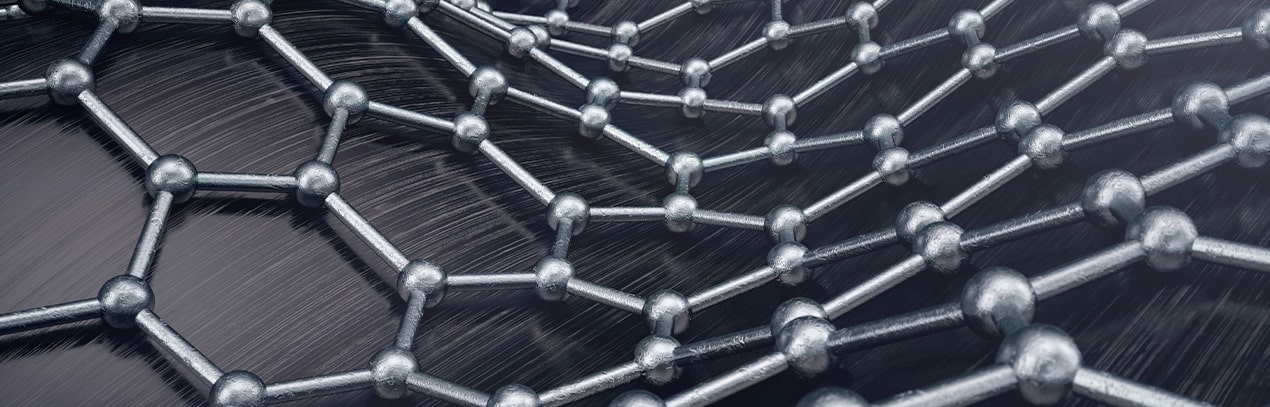
How does graphene oxide improve the performance of polymer fibers?
Graphene oxide is one of the most interesting materials to improve the characteristics of many polymers. It consists of sheets of graphene or pure carbon stabilized with oxygenated groups that make it a multifaceted structure, compatible with water, like cement crystals and easily combinable with other compounds to design materials with new or improved properties, for example:
Distribution within the concrete mix
One of the advantages of graphene oxide designed for the manufacture of polypropylene fibers is its surface chemistry consisting mainly of oxygenated groups (OH- and COOH-) that help maintain the affinity of the fibers with the aqueous elements of the graphene paste. cement acting in a similar way to plasticizing additives, this is because graphene oxide reduces the surface energy of the fibers, facilitating their distribution within the mixture and avoiding aggregates.
Adherence
Another benefit of graphene oxide present in polypropylene fibers is the electrostatic repulsion that it generates between the cement particles; This phenomenon prevents cement agglomeration and increases the degree of fiber-cement interaction by altering the hydration products and increasing their degree of polymerization. In hardened concrete, this effect increases the coefficient of friction so that when a crack displaces a fiber, more load will be required to displace it within the concrete.
Mechanical strength
Graphene oxide increases the tensile and breaking strength of polymers, this is because its elastic modulus (230 GPa) is slightly higher than that of steel and its alloys (190-214 GPa), but comparable to of Zirconia (160-241 GPa) and Cobalt alloys (200-248 GPa), therefore, fibers with graphene oxide have a lower risk of fracture and are more durable than common fibers
Degradation resistance
Polymeric fibers with graphene oxide have a longer useful life because it is a material that differs from many others that deteriorate because of UV radiation, graphene oxide maintains its structural integrity and mechanical properties, in addition, it is chemically inert. and more resistant to corrosive media.
Thermal stability
Graphene oxide increases the thermal stability of polypropylene by forming interconnected bridges or pathways throughout the polymer matrix, improving heat transport.
Drafting: EF/DH
Sources
- Fabrication of graphene oxide/fiber reinforced polymer cement mortar with remarkable repair and bonding properties. J. Mater. Res. Technol. 2023; 24: 9413;
- The incorporation of graphene to enhance mechanical properties of polypropylene self-reinforced polymer composites J. Wang et al. / Materials and Design 195 (2020) 109073;
- Simultaneous enhancement on thermal and mechanical properties of polypropylene composites filled with graphite platelets and graphene sheets. Composites Part A 112 (2018);
- Experimental study on the properties improvement of hybrid Graphene oxide fiber-reinforced composite concrete. Diamond & Related Materials 124 (2022) 108883.
- Upcycling waste mask PP microfibers in portland cement paste: Surface treatment by graphene oxide. Materials Letters 318 (2022) 132238;
- An Experimental Study on the Effect of Nanomaterials and Fibers on the Mechanical Properties of Polymer Composites. Buildings 2022, 12,
- State-of-the-Art Review of Capabilities and Limitations of Polymer and Glass Fibers Used for Fiber-Reinforced Concrete. Materials 2021, 14, 409;
- Mecanismos de desprendimiento explosivo del hormigón bajo fuego y el efecto de las fibras de polipropileno. Estado del conocimiento. Asociación argentina de tecnología del hormigón. Revista Hormigón 62 (2022-2023) 25