Innovation in the production of composite materials:
the use of graphene in pultrusion
Fiber-reinforced polymeric composites are widely used in the aerospace, automotive, naval, and wind power generation sectors due to their lightweight properties and high mechanical strength. These materials are a booming alternative to replace other materials such as metals.
At present there are different methods for the manufacture of fiber-reinforced composites, among which the pultrusion method stands out. A highly efficient and automated method that allows control of process parameters (greater precision and accuracy), reducing variability in the production of parts.
Pultrusion is a production process for reinforced materials where two components can be distinguished, the matrix or continuous phase and the reinforcement or discontinuous phase. The matrix acts as a bonding agent, in which the reinforcement is embedded. The function of the matrix is to transfer the load to the fibers, keep the fibers in their position, prevent the propagation of cracks, provide physical and chemical properties of the composite and also define the temperature range that the composite material can withstand. The matrix is thermosetting or thermosetting (unsaturated polyester, epoxy resins or vinyl-ester resins). On the other hand, the reinforcement has the purpose of adding some property that the matrix does not have, such as increasing mechanical resistance, rigidity, resistance to abrasion or improving its performance when exposed to high temperatures. The reinforcement efficiency is greater, the smaller the size of the particles or the diameter of the fiber and the more homogeneously they are distributed in the matrix. The most used fibers are glass, carbon and aramid due to their high tensile strength.
The pultrusion process (Figure 1) is continuous and is used to manufacture parts with a constant cross section, such as poles, rods, automotive moldings, etc. In the first feeding stage, the reinforcing fibers go through a perforated plate for alignment, then they go through a pre-molding where a fabric is added to reinforce the fiber. Later, in the second stage, the fibers are impregnated with liquid resin and go to a pre-forming stage where the fibers are oriented before entering the mold. In the third stage (molding), the cross section of the part is shaped, and the resin is hardened by applying heat. During the application of heat in the mold, there are three phases: pre-heating of the matrix and reinforcement, activation of the polymerization catalyst and curing of the material. The profile then exits the mold as a thermoset material and passes into a continuous traction mechanism that pulls the material at a constant speed (fourth stage)). Finally, in the fifth stage, a disk saw cuts the profile to the desired length. The profile of the reinforced composite obtained is a completely rigid material, which does not soften and is insoluble with the ability to withstand high temperatures.
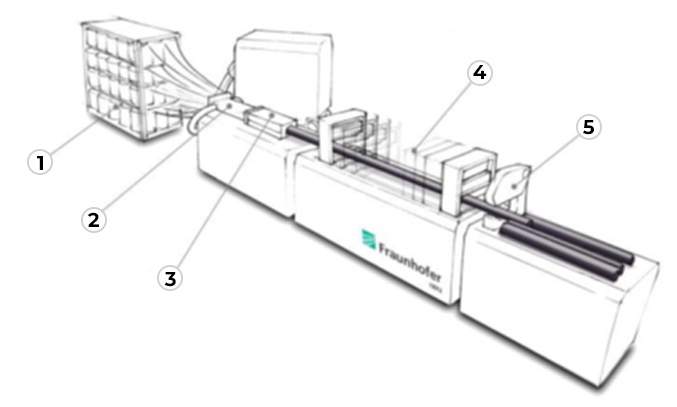
Currently, the main applications of this process are focused on the manufacture of materials for construction, transport, and consumables, for example: vehicle construction, thermal insulation, cable ducts, covers and grids for water treatment plants, beam profiles, building facades, windows, bridges, stairs, among others.
However, there are still limitations in this technology, the low chemical interaction of the fiber with the matrix (resin) leads to a weak interface bond strength between both phases (low chemical adhesion), which makes the behavior of interlaminar shearing and performance of composite materials is not entirely satisfactory. In other words, if the matrix is brittle, spontaneous rupture can be generated. This behavior makes it possible to measure the resistance to interlaminar shearing. Depending on the type of break, the resistance of the matrix material or the quality of the fiber-matrix bond can be characterized.
In recent years, it has been reported that the introduction of functionalized graphene oxide (GO) on the surface of the fibers is an effective method to improve the interfacial properties of composite materials, since the large surface area of graphene oxide allows covering the surface of the fibers, increasing the strength of the chemical bond between the fiber and the matrix, thus improving the mechanical resistance of the reinforced composites. In addition, graphene oxide helps to improve the resistance to interlaminar fracture of the composite material, inhibiting the initiation and propagation of cracks.
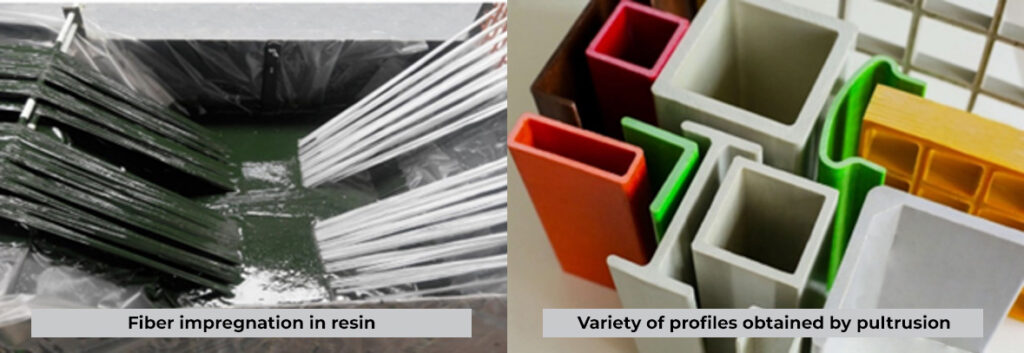
The addition of graphene oxide to reinforced polymeric composites offers numerous advantages for the development of advanced materials in a wide variety of applications due to its large surface area, which has a strong impact on mechanical strength properties, greatly improving properties such as modulus, toughness, and fatigue. On the other hand, graphene oxide can provide compounds with greater resistance to fire. Its efficiency is associated with the fact that graphene oxide has a strong barrier effect, high thermal stability, and great surface absorption capacity, which are favorable for effectively reducing heat and mass transfer.
Currently, Energeia – Graphenemex®, a leading Mexican company in Latin America in the research and production of graphene materials for the development of applications at an industrial level, sells graphene and graphene oxide that can be incorporated or dispersed in any matrix (resin) during the pultrusion process and with them improve the mechanical properties of the profiles or products.
The incorporation of graphene materials (graphene, graphene oxide) in the pultrusion process, provide improvements in the characteristics of the final product, which include:
- Greater tensile strength. Tensile strength can increase up to 30% compared to a standard profile without graphene.
- Production of lighter weight profiles since graphene allows the weight of the product to be reduced without affecting its mechanical properties.
- Profiles with higher modulus of elasticity.
- Greater resistance to corrosion and fire-retardant properties.
- Greater resistance to fractures or fissures.
References
- Yuxin He, Qiuyu Chen. Effect of multiscale reinforcement by fiber surface treatment with polyvinyl alcohol/graphene oxide/oxidized carbon nanotubes on the mechanical properties of reinforced hybrid fiber composites. Composites Science and Technology 204 (2021).108634.
- Jonas H. M. Stiller, Kristina Roder, David Lopitz. Combining Pultrusion with carbonization: Process Analysis and materials properties of CFRP. Ceramics 2023, 6. 330-341.
- Dittrich B, Wartig K-A, Hofmann D, Mu¨lhaupt R, Schartel B. Flame retardancy through carbon nanomaterials: carbon black, multiwall nanotubes, expanded graphite, multi-layer graphene and graphene in polypropylene. Polym Degrad Stab 98:1495.